Gantry cranes, known as Portalkrane in German, have long been the backbone of heavy lifting in industrial environments. These mechanical giants, utilized extensively in shipyards, factories, and construction sites, bridge the gap between efficiency and safety, providing streamlined handling and transfer of heavy materials and loads. This article delves into the intricate world of gantry cranes, offering insights drawn from years of industry experience and supported by expert analysis.
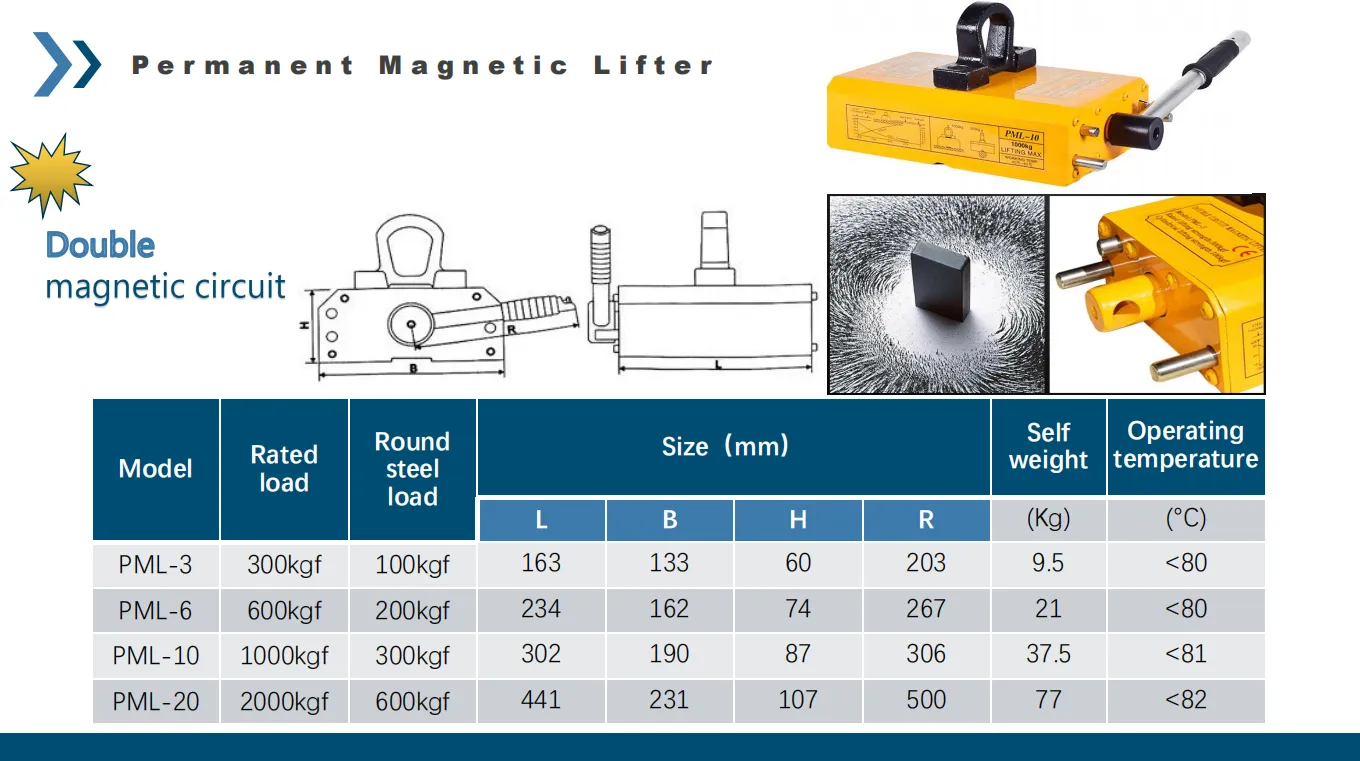
Gantry cranes operate on a structural framework commonly composed of two or more legs fixed to wheels or a track system, allowing mobility and versatility. These cranes are indispensable in environments where overhead cranes are not feasible due to structural or layout constraints. The adaptability of a gantry crane lies in its ability to maneuver expansive areas and its design which is scalable in load capacity and size.
Having witnessed numerous industrial setups, a recurring observation is the significance of choosing the right gantry crane to match operational demands. This choice is pivotal, heavily influencing operational efficiency and safety protocols. Manufacturers provide varied models, each distinguished by its purpose from lightweight designs for small workshops to robust builds for heavyweight industrial applications.
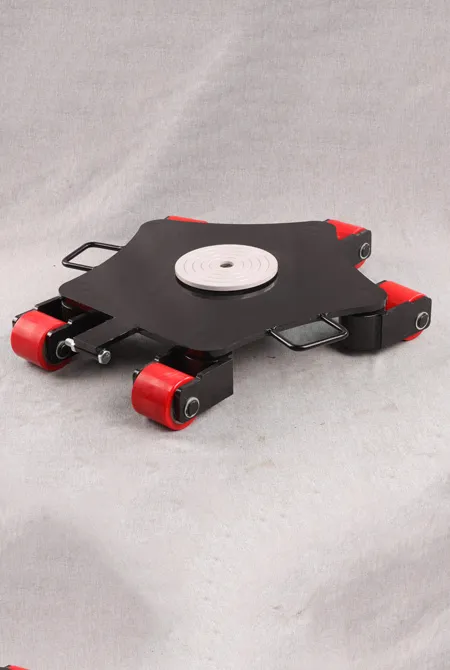
In-depth familiarity with these cranes highlights a few key selection criteria. Material robustness, load capacity, and mobility options are foremost. Gantry cranes are typically constructed from high-strength steel, ensuring durability. The load capacity, often ranging from a few tons to several hundred, should be aligned with the heaviest expected load to avoid overcapacity issues which can lead to operational hazards.
Moreover, the realm of automation has greatly enhanced the capabilities of modern gantry cranes. Integrating automated control systems and precision sensors has drastically reduced human error, leading to enhanced safety. These advancements allow for intricate load management, providing precision in placing loads within millimeters of the intended spot. The data gathered from operating systems also offers critical insights, which when analyzed, help in predictive maintenance—minimizing downtimes and extending equipment lifespan.
gantry crane deutsch
A key element of gantry crane expertise is understanding its functional components. The trolley, hoist, bridge, and legs work in harmony to perform complex lifting tasks. Each component requires routine maintenance to ensure operational safety and longevity. Regular inspections, adherence to load ratings, and monitoring of mechanical and electronic components substantially reduce mishaps and extend the crane's service life.
Authoritative guidance from leading industry figures consistently emphasizes the role of training. Operators and maintenance personnel equipped with thorough training ensure smooth operation and quick troubleshooting. Certification programs, often offered by crane manufacturers, cover detailed aspects of operation, safety standards, and emergency procedures.
Trustworthiness in evaluating gantry cranes involves considering manufacturers with a history of reliability and positive feedback. Renowned manufacturers typically have a proven track record of producing cranes that withstand the test of time under rigorous conditions. Customer testimonials and third-party reviews serve as a credible source of information, reflecting the real-world performance and user satisfaction of these systems.
The future of gantry cranes looks promising, especially with sustainable practices becoming a focal point. Manufacturers are evolving towards eco-friendly designs, incorporating energy-efficient systems without compromising on performance. This trend aligns with global environmental goals, promising reduced carbon footprints and lower operational costs.
In summary, gantry cranes, or Portalkrane, are critical in heavy load management across various industries. Choosing the right crane necessitates understanding its core components, leveraging technological advancements for improved safety and efficiency, and relying on trusted manufacturers for quality assurance. Continuous education and adherence to industry standards further ensure that these mechanical titans continue to operate safely, efficiently, and sustainably, shaping the backbone of modern industrial operations.