Navigating the realm of gantry crane construction unveils a sophisticated intersection of engineering prowess and logistical expertise. At its core, the construction of these cranes revolves around enhancing operational efficiency in numerous industries, including manufacturing, shipbuilding, and port logistics. This article delves into the intricacies of gantry crane construction, encompassing core experiences from the field, expert insights, authoritative guidelines, and trustworthy practices to ensure optimal performance and safety.
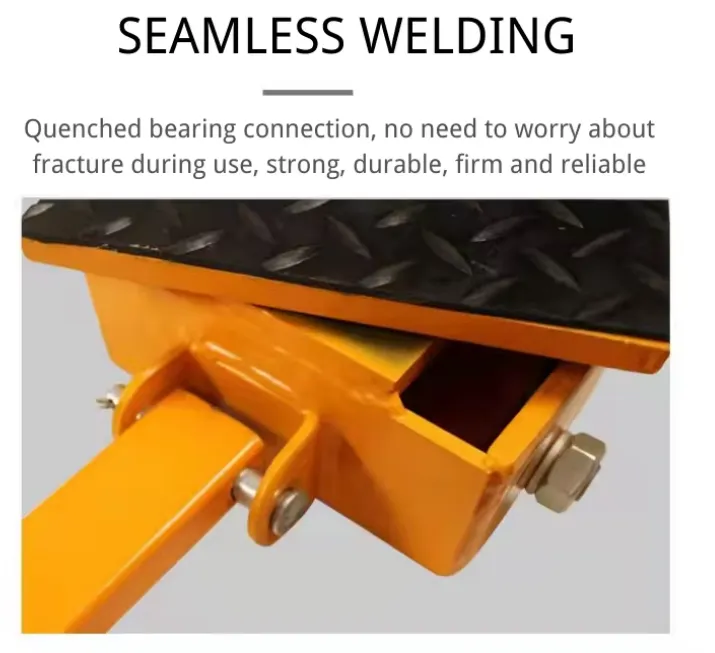
Gantry cranes, characterized by their A-frame structure and overhead beams, serve as indispensable tools in environments requiring heavy lifting and precise maneuverability. Constructing these mechanical giants necessitates a meticulous approach beginning with site analysis. Before initiating construction, evaluating the geographical and environmental conditions is crucial. Each site presents unique challenges; coastal sites may demand corrosion-resistant materials, while inland locations might prioritize temperature variations and seismic resilience.
A breathtaking aspect of modern gantry crane design lies in its modular construction. This approach not only accelerates project timelines but also facilitates maintenance and upgrades. Modular gantry crane components are prefabricated in controlled environments, ensuring uniformity, quality, and adherence to strict safety standards. The assembly process on-site is streamlined, requiring only efficient logistical coordination and experienced manpower.
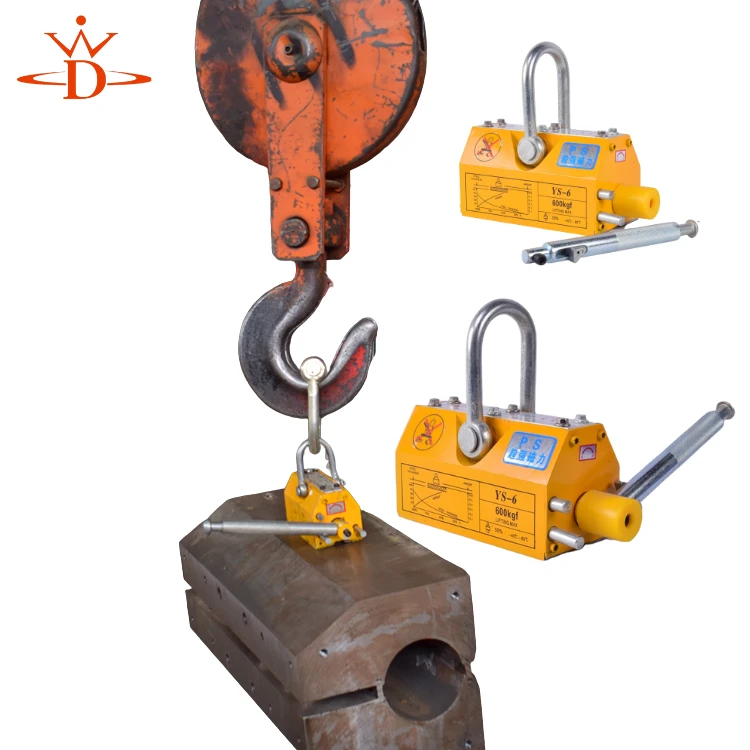
From an expertise perspective, engineers must specify materials that align with the intended operational lifecycle of the gantry crane. High-tensile steel is frequently chosen for its durability and strength-to-weight ratio—critical factors in mitigating the stress endured during heavy lifting tasks. Additionally, engineers often incorporate innovative technologies such as load moment indicators, anti-sway systems, and remote control operations to enhance safety and precision.
gantry crane construction
Authoritativeness in gantry crane construction is reinforced through adherence to internationally recognized standards such as those set by the American Society of Mechanical Engineers (ASME) and the Occupational Safety and Health Administration (OSHA). Compliance with these standards not only guarantees structural integrity but also fosters a safety-first culture that protects workers and assets.
Gaining trust within the industry hinges upon the reliability and performance history of gantry cranes. Regular maintenance schedules, combined with comprehensive training programs for operators, establish a circle of trust among stakeholders. Operators trained to handle emergency scenarios, coupled with routine inspections, diminish the risks of operational failures and extend the service life of the cranes.
Experience on the ground reveals that successful gantry crane construction projects are underpinned by robust project management. Coordinating between engineering teams, suppliers, and on-the-ground construction workers requires adept managerial skills. Real-world experiences emphasize the importance of transparent communication channels and adaptive strategies that account for unexpected delays or site-specific challenges.
In conclusion, the construction of gantry cranes represents a potent blend of engineering capabilities and industry expertise. By embracing cutting-edge design principles, adhering to authoritative safety standards, and cultivating a culture of trust through reliability and transparency, industry leaders can construct gantry cranes that elevate operational productivity and meet the demands of modern industrial landscapes.