Gantry girders are an essential component in many industrial and construction projects, playing a crucial role in supporting crane systems and enabling the smooth transportation of heavy loads. Selecting the right type of gantry girder is a decision that requires careful consideration of several factors, including the operational context, load requirements, and structural conditions. Here is a detailed examination of various types of gantry girders to guide industry professionals in making informed decisions.
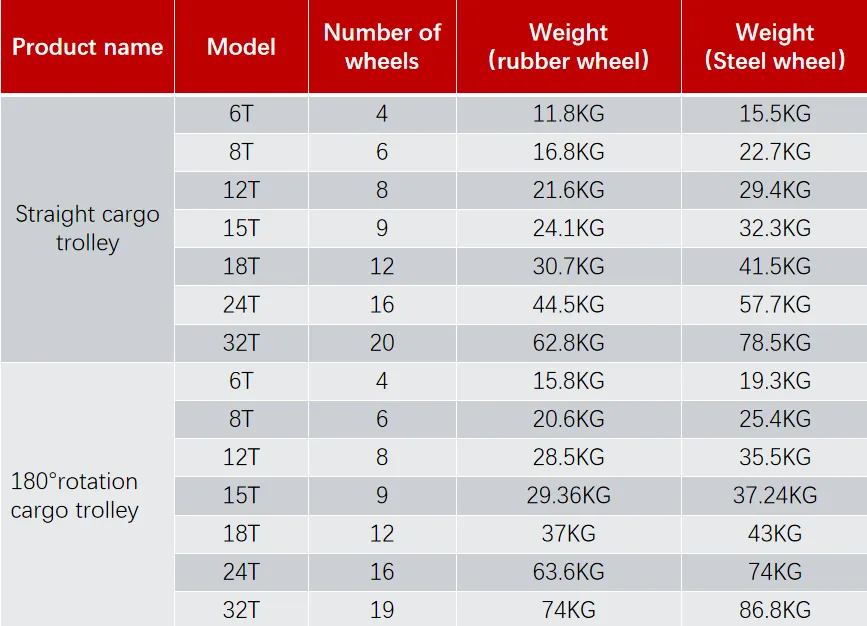
The most basic classification of gantry girders relies on their construction material. Predominantly, these are made from steel due to its excellent strength and durability. However, variations exist based on the specific use case.
1. Rolled Steel Gantry Girders These are typically made from standardized sections such as I-beams or H-beams. Their simple design makes them cost-effective and easy to manufacture, which is beneficial for projects with budget constraints. Nevertheless, they may not provide the necessary strength for applications involving extremely heavy loads or large spans.
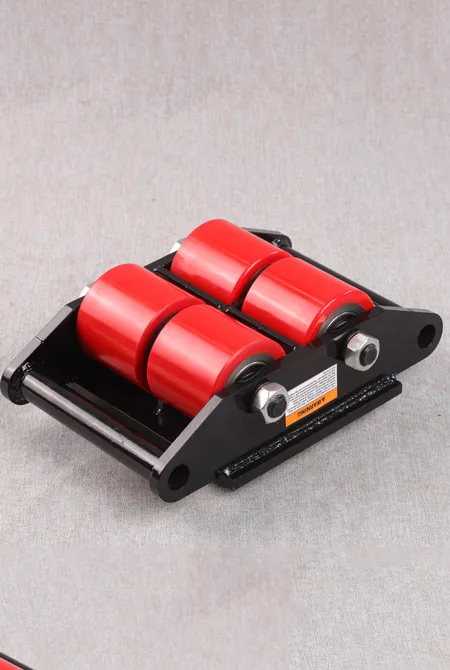
2. Built-up Steel Gantry Girders To extend beyond the limitations of rolled sections, built-up girders are assembled using plates and other structural components. This type of gantry girder allows for customization according to specific load and span requirements, making them ideal for heavy-duty applications. Their construction requires precision engineering and expertise, ensuring that they meet the rigorous safety and performance standards expected in industrial environments.
3. Box Type Gantry Girders Offering high torsional rigidity and structural stability, box type girders are essentially hollow rectangular sections. They are capable of handling higher loads and resisting sway caused by lateral forces. Industries that deal with heavy cranes or operate in environments prone to lateral movements, such as coastal areas subject to wind or seismic activities, may find this type valuable.
4. Composite Gantry Girders This design incorporates different materials, typically a combination of steel and concrete. The concrete is usually reinforced, enhancing the girder’s ability to handle compressive forces, while the steel provides tensile strength. The composite girder balances cost with performance, offering economic benefits without sacrificing structural integrity.
A more nuanced understanding of gantry girders involves consideration of their configuration and application
types of gantry girder
1. Single Girder Configurations These involve only one girder supporting the crane and are typically used in lighter applications. Single girder configurations are easier to install and require less ongoing maintenance, which can be advantageous for facilities needing efficient operations with minimal interruption. However, their lower load capacity may limit their usefulness in some industries.
2. Double Girder Configurations For operations requiring greater load capacities, double girder configurations are the preferred option. With two girders supporting the crane, the system can handle much greater weights, making it suitable for heavy industrial usage. This configuration supports longer spans and higher lifts, offering flexibility for diverse operational needs.
3. Semi-Gantry Systems In certain scenarios, a full gantry frame might be unnecessary or impractical. Semi-gantry systems, which involve one end of the girder supported by the ground and the other by an elevated structure, provide a space-saving and cost-effective solution. This design is particularly useful in environments where space is limited or where overhead clearance is a concern.
4. Full Gantry Systems These encompass full-frame structures where the crane runs on wheels situated on both sides of the girder, providing complete mobility and range. Full gantry systems are suitable for outdoor applications, such as shipyards or factories manufacturing large products, where full access around the load is required.
Choosing the right gantry girder type demands a detailed understanding of the specific project requirements and site conditions. Factors like load capacity, installation environment, budget constraints, and future scalability should all influence the decision-making process. Moreover, consulting with structural engineers and using advanced simulation software can further aid in optimizing the design of gantry girders to ensure safety and efficacy.
In practice, the successful use of gantry girders also hinges on rigorous compliance with industry standards and regular inspections. This ensures not only the longevity of the gantry girder itself but also the overall safety and efficiency of the operational setup.
By comprehensively evaluating these aspects, industry experts can assure the implementation of the most suitable gantry girder solution, driving productivity and safety in their respective fields. This strategic approach solidifies credibility and fosters trustworthiness with clients and stakeholders.