Types of Gantry Girder A Comprehensive Guide for Modern Construction
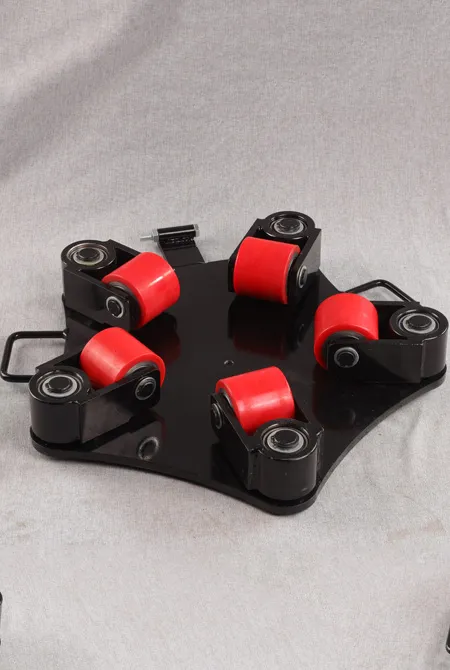
Gantry girders are pivotal in industrial settings, providing robust support for overhead cranes that transport heavy materials across manufacturing floors, construction sites, and shipyards. Understanding the different types of gantry girders is crucial for engineers, architects, and contractors seeking to optimize functionality, safety, and cost-effectiveness in their projects. This guide explores the diverse types of gantry girders, highlighting their unique attributes, applications, and the engineering principles that underscore their designs.
1. Single Girder Gantry Crane Simplicity Meets Efficiency
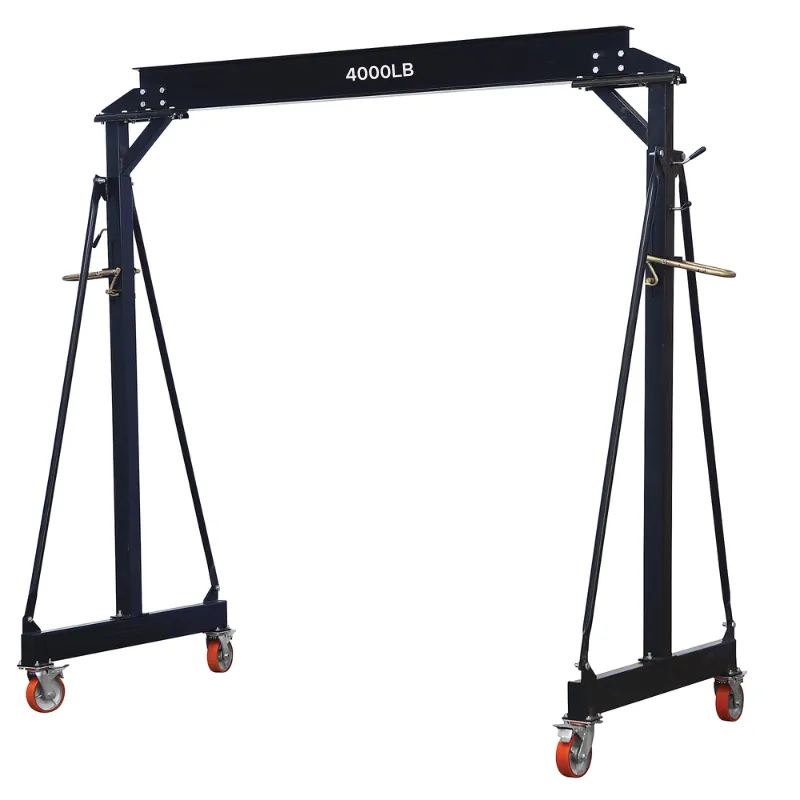
Single girder gantry cranes feature a single bridge beam supported by end trucks. Their straightforward design makes them ideal for light to moderate lifting in small to mid-sized facilities. They offer cost advantages due to fewer materials and simpler construction requirements. Their lower headroom is beneficial in facilities with height restrictions. However, the simplicity of single girder models should not mislead; they are engineered with precision to deliver dependable performance, characterized by a lightweight structure that simplifies installation and maintenance while ensuring durability.
2. Double Girder Gantry Crane Unmatched Load Capacity
When the task demands moving hefty loads across vast spaces, double girder gantry cranes step in with their two bridge beams that significantly enhance load-bearing capacity.
This type provides a greater hook height, enabling taller lifts. The robust structure allows for supplemental equipment such as lights, platforms, or walkways to be added, enhancing operational flexibility. While requiring more extensive planning and engineering due to their complexity and cost, double girder models are indispensable in shipyards, steel mills, and other heavy-duty industrial environments.
3. Box Girder Gantry Crane The Epitome of Strength
types of gantry girder
Renowned for their structural integrity, box girder gantry cranes incorporate a welded steel box in their design, offering superior torsional rigidity. This robust construction is ideal for environments subject to frequent, heavy lifting and harsh conditions. Box girders accommodate longer spans and greater load demands without flexing, thus minimizing operational risks and maintenance demands. Industries such as aerospace and automotive manufacturing benefit from the high precision lifting these girders provide, paired with reduced deflection and enhanced stability.
4. Truss Girder Gantry Crane Mastering Outdoor Applications
Truss girder gantry cranes are constructed with a truss beam, making them lightweight yet exceptionally strong. Their design excels in outdoor settings, where wind loading is a critical consideration. The truss structure effectively distributes weight and reduces the wind resistance, making it useful in yard operations and construction sites. The economic use of material in truss girders often translates to cost benefits, without compromising on performance or reliability.
5. Portable Gantry Crane Flexibility Redefined
Portable gantry cranes offer unparalleled mobility and ease of maneuverability, catering to industries that require relocation of lifting solutions. Typically smaller in scale and designed for lighter loads, they are frequently used in workshops and garages. Their design focus on ease of assembly and disassembly ensures quick deployment, making them an adaptable solution for dynamic work environments. Despite their simplicity, portable gantry systems are crafted to adhere to rigorous safety standards, ensuring reliable lifting wherever needed.
Each type of gantry girder serves a specific purpose, guided by factors such as load capacity, span length, environmental conditions, and budgetary constraints. Selecting the appropriate gantry girder requires a nuanced understanding of these variables, coupled with comprehensive project evaluation and professional guidance. Prioritizing engineering excellence, safety standards, and innovative design ensures that gantry girders continue to be indispensable in the infrastructure of industrial efficiency.
Staying abreast of the latest advancements in materials, technology, and design can further optimize the application of gantry girders. Collaboration with leading engineers and manufacturers is essential to harness new innovations that promote sustainability, enhance performance, and ensure compliance with evolving industry regulations. Gantry girders, in their multifaceted forms, remain a cornerstone of industrial operations, enabling safe and efficient material handling in diverse and challenging environments.