Small lifting magnets are quintessential tools in diverse industrial applications, thanks to their unique ability to move objects with remarkable precision and efficiency. Understanding their potential not only enhances operational productivity but also ensures safety and reliability in handling materials in varied environments.
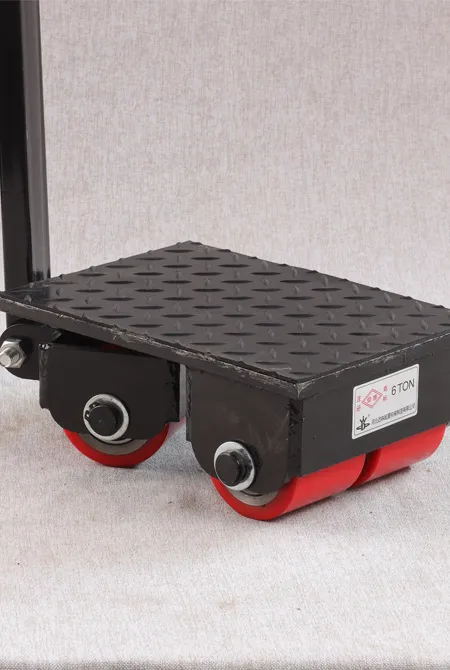
Small lifting magnets are ingeniously crafted to lift ferrous metal objects using the magnetic force generated through electricity or permanent magnetism. They reduce manual handling, thereby lowering the risk of injuries and optimizing time in moving metal components. This innovative manipulation of magnetic fields makes these magnets invaluable across sectors such as construction, manufacturing, automotive, and shipping.
Experience in utilizing small lifting magnets reveals that these tools can manage a broad spectrum of weights and sizes. From lifting small components in manufacturing plants to handling larger sheets of metal in shipyards, they are versatile assistants. Users of small lifting magnets can testify to their surprisingly robust lifting power, sometimes lifting up to thousands of pounds depending on the design and power of the magnet. Furthermore, employing these magnets eliminates the need for slings, hooks, or chains, thereby reducing potential damage to the lifted materials and increasing the process's overall efficiency.
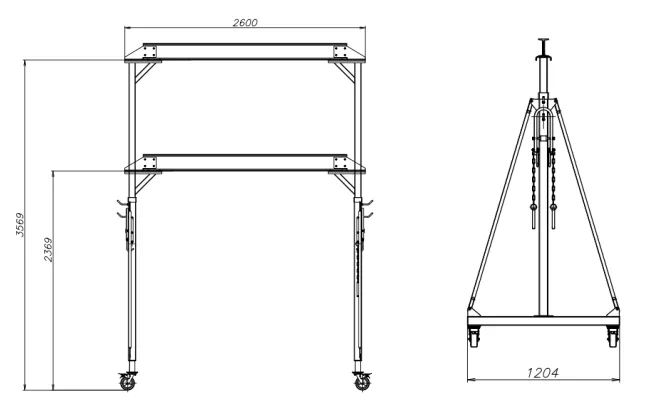
Expertise in the field underscores the importance of selecting the right type of small lifting magnet for the task.
There are primarily two types permanent lifting magnets and electro lifting magnets. Permanent magnets are suitable for operations requiring constant strength without the need for an electrical power source. They are typically smaller and lightweight, making them easy to integrate into manual processes. On the other hand, electro lifting magnets are preferred for tasks that require variable magnetic force. These magnets can be turned on and off as needed, providing greater control and flexibility in handling different materials or achieving specific lift capacities.
small lifting magnets
Understanding the intricacies of electromagnetism and magnet count coefficients renders an indispensable insight into these devices' efficacy. Regular testing and maintenance help in minimizing wear and tear, ensuring consistent performance and prolonging the magnet's life span. Best practices involve conducting periodic inspections and testing with certified equipment to maintain the highest safety standards.
Authoritativeness in the domain of small lifting magnets is echoed by industry leaders and safety organizations that advocate for stringent adherence to operational guidelines. As these magnets are pivotal in lifting operations, global bodies such as the International Organization for Standardization (ISO) and the American National Standards Institute (ANSI) regulate their deployment and usage. Compliance with these standards guarantees not only the efficiency of lift operations but also assures stakeholders of operational safety, reducing risks associated with mechanical failures.
The trustworthiness of small lifting magnets is cemented by documented case studies and reviews from end-users across industries. Real-world scenarios often illustrate how these tools have transformed material handling operations, contributing significantly to improved safety records, cost-effectiveness, and productivity. For instance, in automotive manufacturing, small lifting magnets have streamlined assembly lines by speeding up the transfer of metal parts without compromising safety or precision. The testimonials from industry practitioners stand as testament to the reliability and performance of small lifting magnets.
In conclusion, small lifting magnets represent an essential investment for industries reliant on efficient and safe material handling. Their application not only advances industrial processes but also provides a benchmark for safety and reliability. For businesses looking to implement or upgrade their material handling capabilities, understanding the dynamics of small lifting magnets and adhering to recommended standards is crucial. As technology advances, the evolution of lifting magnets is likely to introduce further innovations, creating even more opportunities to enhance efficiency and safety in industrial settings.