Moving heavy equipment is a task that demands efficiency, safety, and reliability. For businesses and industries relying on the seamless relocation of cumbersome machinery, rollers specifically designed for moving these heavy loads are indispensable. Drawing from my extensive experience and expertise in industrial relocation, this article delves into the pivotal aspects of rollers as a tool, ensuring you make an informed decision.
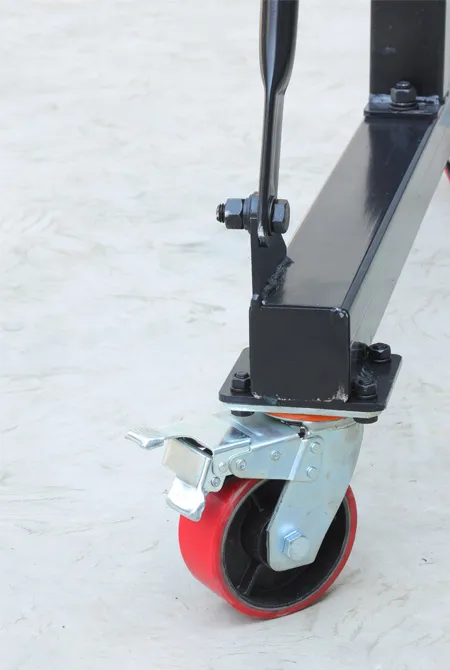
A common issue when relocating hefty equipment is the potential for damage to both the items being moved and the surfaces upon which they are rolled. This is where specialized rollers come into play, offering a credible solution by evenly distributing the weight, which minimizes floor damage and ensures the safety of the equipment. The design and engineering behind these rollers are intricate, focusing on durability, load-bearing capacity, and maneuverability.
Attention to material choice within the roller construction is critical for expertise in this domain. Most high-quality rollers are composed of steel with a polyurethanic or rubber coating. Steel offers the unparalleled strength necessary for handling tons of weight, while the coatings provide friction reduction and floor protection. This combination is a hallmark of trustworthiness and should be non-negotiable in any reliable roller choice.
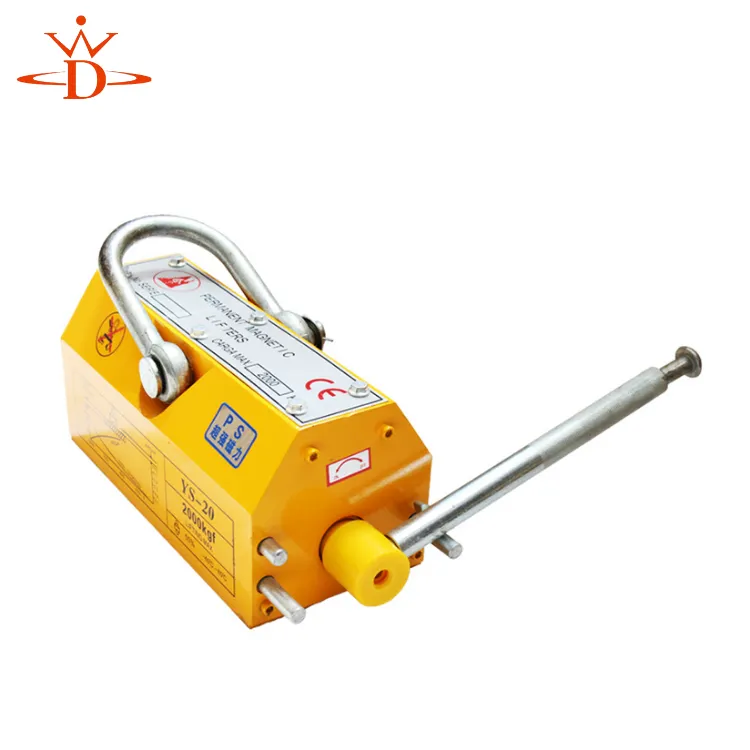
Expertise in selecting the correct roller size and type cannot be overstated. A profound understanding of the weight specifications and the nature of the equipment being moved is essential. For instance, smaller, compact rollers might be ideal for maneuvering in tight spaces, whereas larger, more robust versions may be suited for expansive areas with heavier equipment. It's crucial to align the roller's capabilities with specific industrial needs for optimal performance.
rollers for moving heavy equipment
Moreover, these rollers are not just essential for traditional industrial environments but have also proven to be authoritative tools in emerging tech-oriented facilities. Data centers needing server rack repositioning, for example, benefit greatly from rollers that ensure a swift, damage-free move. Similarly, in manufacturing and production lines, minimizing downtime during machinery relocation could lead to increased productivity and reduced costs.
Trustworthiness in this field also necessitates understanding the mechanics behind roller designs. For enhanced safety, many rollers are equipped with steering handles, swivel casters, or brakes, providing greater control over movement and direction. This specificity in design ensures that even novice operators can move equipment with confidence, reducing the risk of accidents.
A crucial aspect of selecting the right roller is not only understanding current load requirements but also allowing for future scalability. Businesses in growth often find their initial purchases become obsolete as their equipment size or quantity increases. Therefore, investing in rollers with a higher weight capacity than currently required can avert the need for new purchases in the short term, reflecting an expert foresight in equipment management.
In conclusion, the nuanced use of rollers for moving heavy equipment is integral to numerous industries, influenced by material choice, size, design, and future scalability. These factors collectively ensure safety, efficiency, and cost-effectiveness. Guided by experience and a robust understanding of the needs across various sectors, selecting the right rollers involves weighing these critical components to ensure seamless operations. Consider these insights when choosing your next set of rollers, assuring both immediate and long-term industrial harmony.