Overhead gantry systems are revolutionizing the way industries manage and streamline their operations, offering unparalleled efficiency and precision in various applications. These structures stand tall in manufacturing plants, logistics centers, and transportation hubs, serving as the backbone for a range of automated processes.
With the rise of Industry 4.0 and the increasing demand for intelligent infrastructure, investing in overhead gantries has become a strategic move for future-ready businesses.
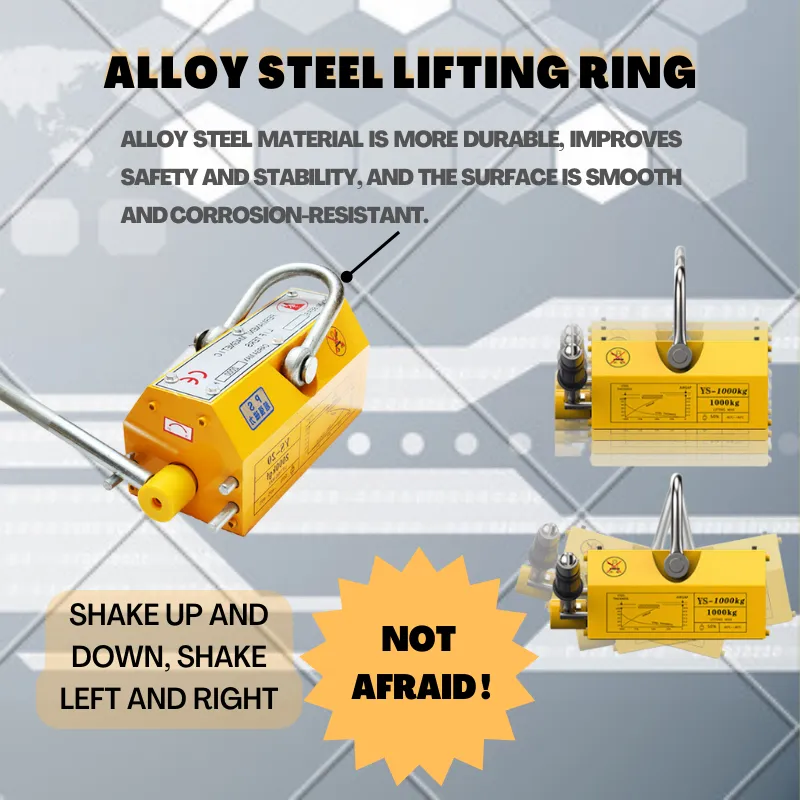
The expertise behind designing and implementing overhead gantries cannot be overstated. These systems are meticulously engineered to handle heavy loads while maintaining seamless automation. Typically constructed from robust materials such as aluminum or steel, they boast high strength-to-weight ratios, crucial for sustaining prolonged operations under demanding conditions. A well-designed gantry system integrates advanced software controls, responsive sensors, and precision mechanics, providing a synchronized environment where efficiency meets productivity.
Industry leaders champion the authoritativeness of overhead gantries due to their customizable features. From simple monorail designs to complex multi-axis configurations, these systems adapt to specific requirements, enhancing workflow without necessitating a complete overhaul of existing facilities. This modularity ensures that businesses can scale operations efficiently, adding or modifying components as demand fluctuates. Moreover, integrating overhead gantries with existing IT infrastructure, such as warehouse management systems and ERP solutions, offers real-time data acquisition and analytics, paving the way for improved decision-making and operational agility.
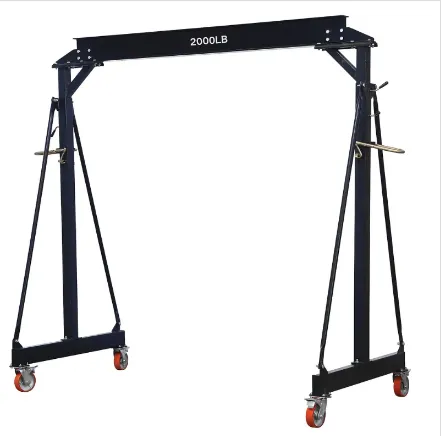
Trustworthiness is embedded into every facet of these robust systems. Safety is paramount, with state-of-the-art safety protocols and fail-safes equipped to mitigate risks and ensure worker protection. Regular maintenance, coupled with rigorous testing protocols, ensures that each gantry system operates at optimal capacity, minimizing downtime and potential operational bottlenecks. For organizations, this translates into increased confidence and peace of mind, knowing that their overhead gantry systems meet and often exceed industry safety standards.
overhead gantry
The real-world experiences of implementing overhead gantry systems reveal transformative impacts. Many businesses have experienced a marked increase in throughput and a significant reduction in manual handling costs. For instance, automotive assembly lines employing overhead gantries report enhanced accuracy in part positioning, reducing wastage and rework. In the logistics sector, gantries have streamlined the movement of goods in warehouses, optimizing storage and retrieval times, thus speeding up the entire supply chain.
Presence in diverse sectors—from aero manufacturing to food and beverage industries—demonstrates the versatility and indispensable role of overhead gantries. As businesses continue to seek solutions that enhance productivity while ensuring sustainability, these systems remain at the forefront, offering eco-friendly options by reducing energy consumption and supporting green logistics practices.
Future advancements in overhead gantry technology promise further improvements. Integrating Artificial Intelligence and the Internet of Things (IoT) into gantry systems will undoubtedly elevate functionality, allowing predictive maintenance and autonomous operations. As organizations increasingly prioritize efficiency and sustainability, overhead gantries are set to remain integral to both current operational demands and future innovations.