Magnetic lifters have emerged as indispensable tools in various industrial sectors due to their exceptional ability to efficiently handle heavy ferrous loads. These devices have revolutionized the way industries operate, especially in material handling, metalworking, and warehousing, offering time-saving, safe, and economical solutions.
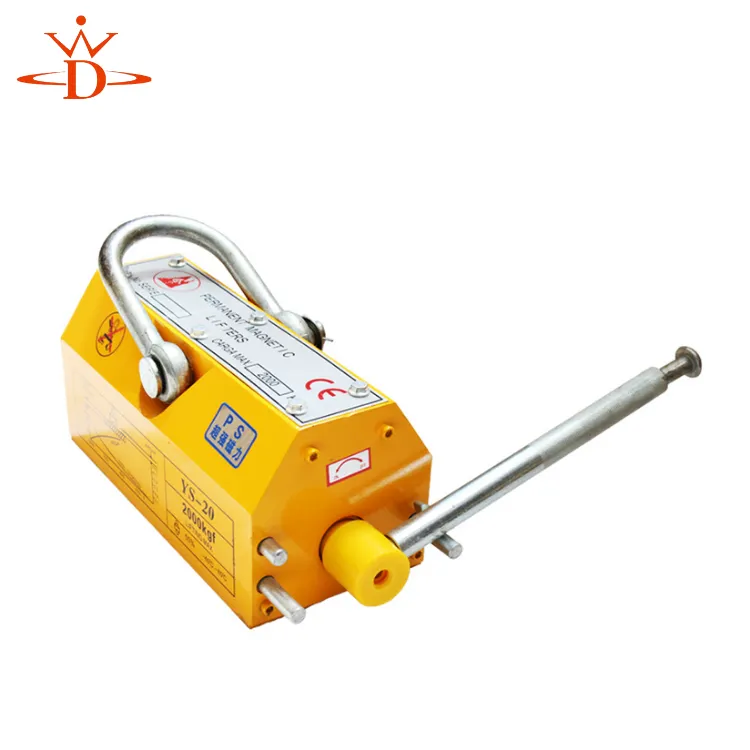
Built upon the principle of magnetism, magnetic lifters operate without the need for electricity or any other external power source, which makes them not only eco-friendly but also highly reliable in environments where uninterrupted power supply may be an issue. The simple mechanical design,
often featuring a durable magnetic circuit, ensures minimal maintenance. This ease of use extends the device’s operational lifetime, providing an added advantage for companies looking to maximize productivity while minimizing costs.
The expertise in using magnetic lifters involves understanding the nuances of their strength and application. Typically, a magnetic lifter can handle flat materials like steel plates or rounds. Professionals adept in their use often consider the surface conditions—rust, paint, and roughness can affect the gripping strength. Therefore, regular assessment of the load surface is vital. Additionally, knowing the weight limitations of the particular model in use ensures safety, as exceeding the threshold can negate the magnetic grip, potentially leading to accidents.
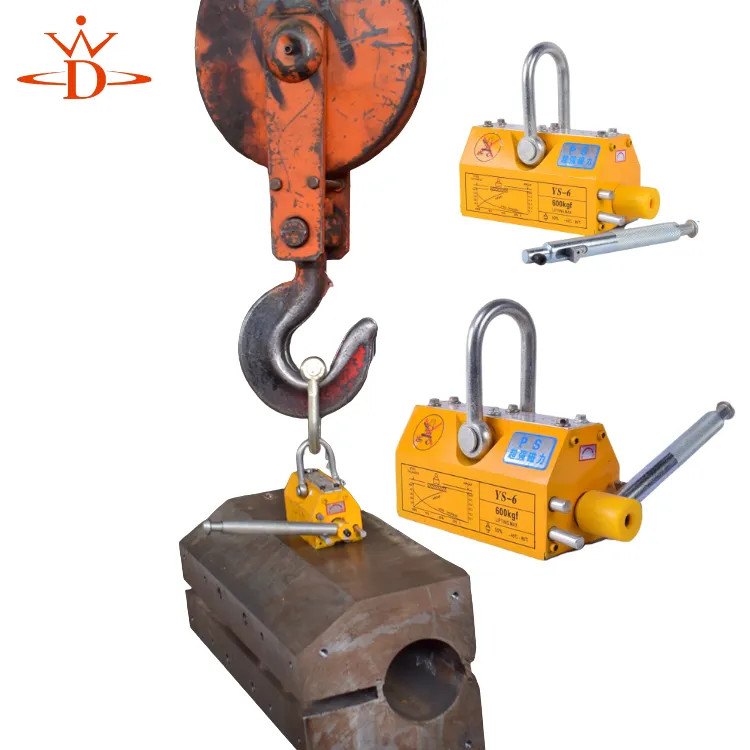
In industries like shipbuilding, automotive, and construction, where large metal components are commonplace, magnetic lifters provide invaluable support. Their ability to lift and move components without deforming or causing surface damage is key in maintaining the integrity of parts, which is crucial for the precision required in these fields. Moreover, their implementation reduces the labor costs associated with traditional lifting equipment, such as chains or slings, which often require multiple operators.
magnetic lifter
Trust in magnetic lifters comes from their proven track record. Case studies have demonstrated that businesses that incorporate these devices witness a significant reduction in workplace injuries related to manual lifting and handling. Furthermore, given that magnetic lifters don't rely on electricity, they eliminate the risk of shocks or electrocution, making them a safer option in diverse working environments.
Further enhancing their trustworthiness is the regulatory compliance of magnetic lifters with safety standards. Many models undergo rigorous testing and certification processes to ensure they meet or exceed industry-specific safety standards, offering peace of mind to operators and businesses alike. It is crucial, however, for users to adhere strictly to operating guidelines and routinely inspect the device for wear and tear, ensuring ongoing reliability.
One pivotal aspect that contributes to the authoritative stance of magnetic lifters in industrial settings is the technical support and training provided by manufacturers. Leading manufacturers often offer comprehensive training programs to ensure that businesses not only use magnetic lifters effectively but also integrate them into their safety protocols. This emphasis on education underscores the commitment to a safe and proficient workplace.
In conclusion, magnetic lifters exemplify a balance between innovative engineering and practical application. Their role in enhancing operational efficiency and safety elevates them to a preferred choice for metal handling. For any business considering an investment in material handling equipment, understanding the capabilities, limitations, and safety guidelines of magnetic lifters will ensure they harness these devices' full potential, ultimately leading to optimized productivity and safety in their operations.