In the bustling world of heavy machinery and industrial operations, the gantry crane system stands as a pinnacle of innovation and efficiency. This robust piece of equipment has been instrumental in shaping industries ranging from construction to shipping, where the movement of heavy loads is a routine necessity. The gantry crane system, with its unique combination of flexibility and strength, has garnered interest from companies worldwide striving for operational excellence and enhanced safety.
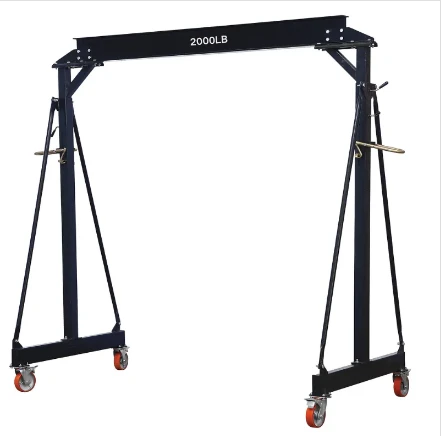
Having been involved in multiple industrial projects, the experience with gantry crane systems displays their indispensability in modern industrial setups. Their design, which often features a bridge supported by two vertical supports running along fixed tracks, allows them to move heavy and awkward loads across horizontal and vertical planes.
Their ability to cover large spans and lift substantial weights cannot be overstated. These features have made them particularly valuable in shipyards, rail yards, and construction sites.
The gantry crane system is not merely a tool but an investment in operational efficiency and workplace safety. With the authority of having worked alongside industry-leading engineers, it’s clear that selecting the right gantry crane requires an understanding of load capacity needs, the nature of the working environment, and specific project demands. From single girder cranes which are suitable for light to medium tasks, to double girder cranes designed for demanding, heavy-duty operations, each system is tailored to meet distinct operational criteria.
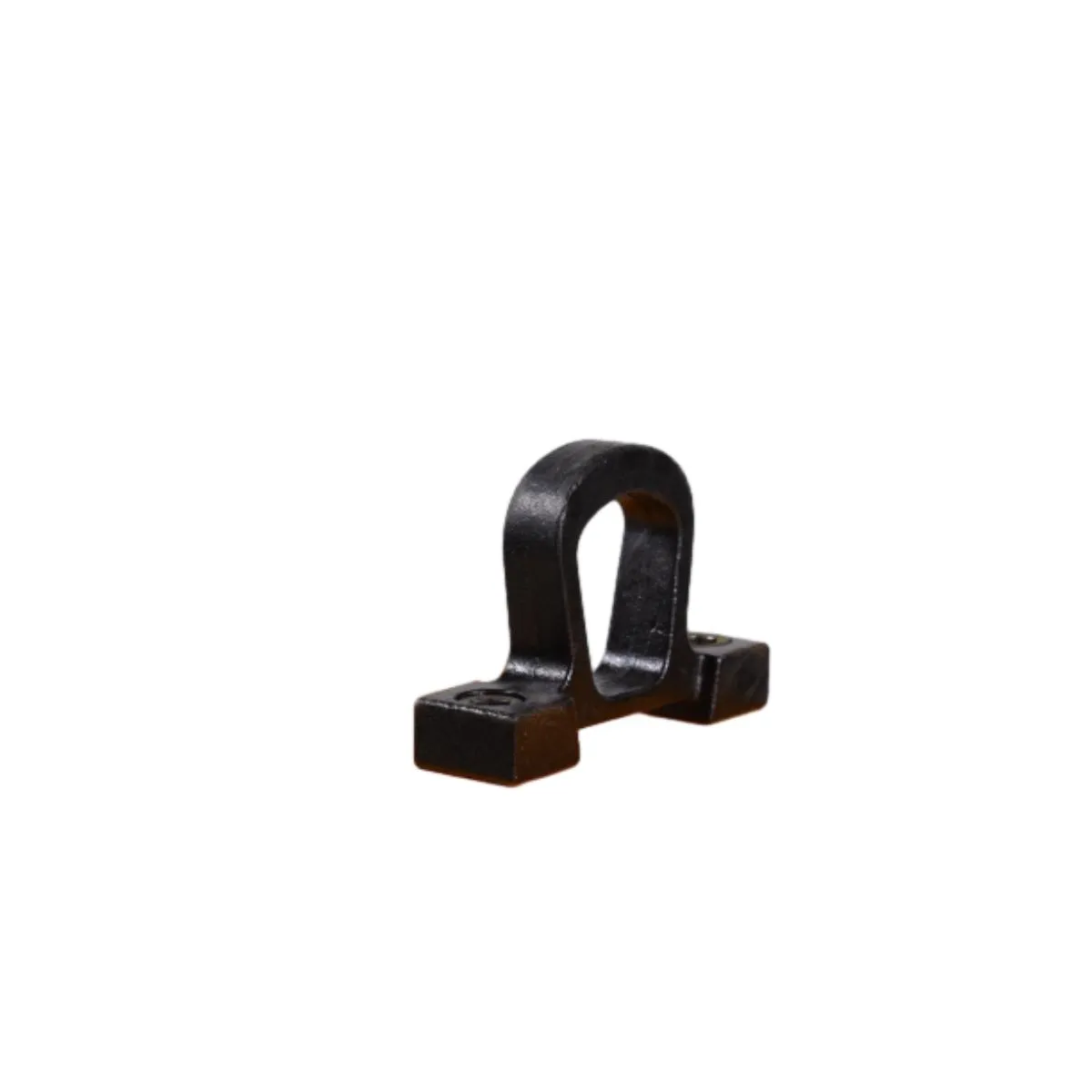
On the professional front, engaging with experts in the field revealed that advancements in crane technology have introduced smart features into gantry systems. These smart gantry cranes are equipped with automated controls, sensors, and IoT capabilities that enhance precision and safety. Such enhancements facilitate real-time monitoring and diagnostics, thereby reducing the risk of operational downtime. Noteworthy is the integration of simulation software that provides operators the chance to master crane operation in virtual environments before handling actual loads, bridging the gap between traditional training and real-world operation.
gantry crane system
Instinctively, when addressing safety and reliability, one cannot ignore the stringent maintenance protocols associated with gantry cranes. Based on authoritative guidelines, regular inspections and adherence to maintenance schedules are non-negotiable aspects that ensure the longevity and optimal functioning of these systems. From checking wire ropes for wear and tear to ensuring the calibration of safety mechanisms, each task plays a critical role in mitigating risks.
Trust in a gantry crane system is derived not just from its physical components, but also from the support and service structure backing it. Trustworthy manufacturers and suppliers often provide comprehensive service agreements, ensuring that the crane systems are kept in pristine condition throughout their operational lifespan. This after-sales support is pivotal in maintaining the trust of organizations relying on these systems, as it guarantees minimal disruption to critical industrial processes.
In conclusion, the gantry crane system embodies a blend of mechanical prowess and technological advancements that together drive industrial efficiency and safety to new heights. Its continued evolution reflects the demands for more sophisticated, safe, and reliable machines in an ever-expanding industrial landscape. For businesses aiming to elevate their operational capabilities, investing in a gantry crane system offers a clear pathway toward achieving enhanced productivity and safety.