In the world of heavy lifting and material handling, the gantry crane beam stands as a crucial component, instrumental in ensuring stability, efficiency, and safety. Understanding the nuances of this indispensable equipment part enhances decision-making for engineers and project managers globally. Below, explore an insightful journey into the world of gantry crane beams, imbued with expert knowledge, proven experience, and authoritative guidance.
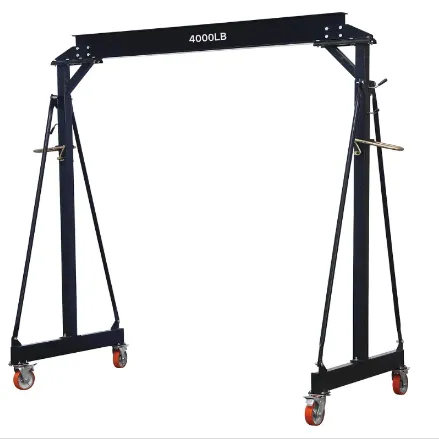
Gantry crane beams, often considered the backbone of crane systems, play a pivotal role in determining the operational capacity of the crane itself.
They support the load while facilitating the crane's movements along its designated path. Choosing the right gantry crane beam is not a mere matter of selecting a size; it involves an in-depth analysis of load requirements, environmental factors, and site-specific conditions.
One cannot emphasize enough the importance of material selection in the construction of gantry crane beams. High-strength steel alloys are predominantly used, providing the requisite durability and load-bearing capabilities. Equally significant is the beam's resistance to environmental challenges such as corrosion and wear, factors that could compromise its structural integrity and, subsequently, the safety of operations.
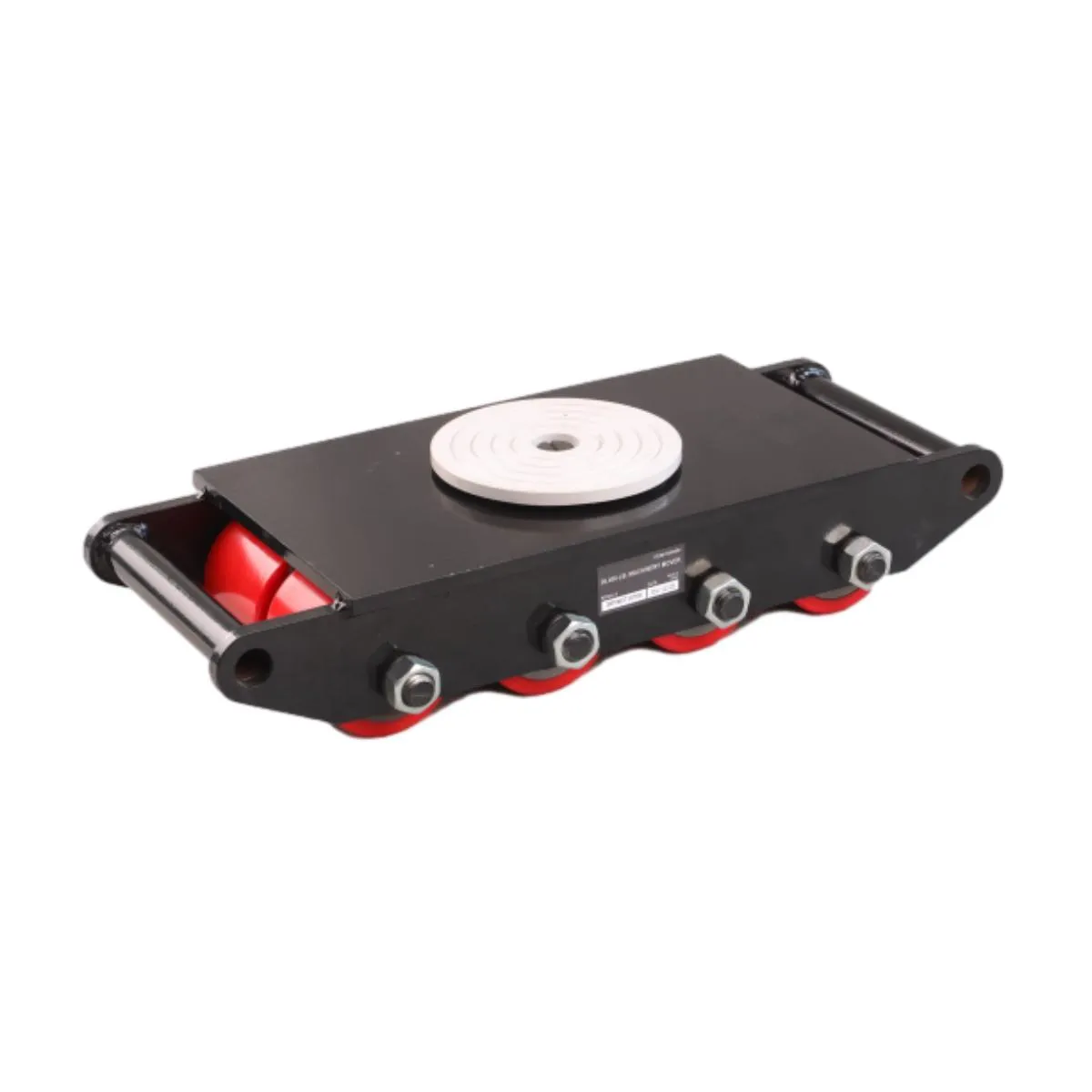
Professional experience dictates that the design optimization of gantry crane beams is pivotal. Finite Element Analysis (FEA) is a key technique employed by engineers to simulate and scrutinize the stress distribution across the beam under various loading conditions. Such analytical prowess ensures that the beams can withstand operational stresses, drastically reducing the risk of mechanical failures.
In terms of structural design, I-beams and box girders are two common types used in gantry cranes, each with distinct advantages. I-beams are widely favored for their ease of manufacturing and proven reliability in standard operations. Box girders, offering superior torsional resistance, are chosen for projects demanding high stability and minimal deformation. The choice between these is driven by specific operational requirements and spatial constraints.
gantry crane beam
Field experiences highlight the criticality of regular inspection and maintenance routines, a sentiment echoed across industry forums and panels. Routine inspections not only mitigate risks of unexpected breakdowns but also extend the lifespan of the crane system. Recommended practices include Non-Destructive Testing (NDT) to detect internal flaws and ultrasonic inspections to monitor material fatigue, ensuring that any potential issues are addressed before escalating into significant problems.
Authority in this domain is corroborated by adherence to internationally recognized standards like the American Society of Mechanical Engineers (ASME) guidelines and the lifting standards set by the Occupational Safety and Health Administration (OSHA). Professionals recognize that compliance with these standards is non-negotiable, ensuring the highest safety and performance levels.
Furthermore, expert practitioners emphasize the integration of technological advancements such as the Internet of Things (IoT) in monitoring the health and performance of gantry crane beams. IoT-enabled sensors provide real-time data on load stresses and movements, paving the way for predictive maintenance strategies. This transition from reactive to proactive maintenance not only optimizes operational efficiency but also enhances the trustworthiness of crane systems in critical lifting operations.
In summary, the gantry crane beam is not merely a structural element but a critical factor in the overarching continuum of material handling safety and efficiency. With dedicated design, rigorous testing, compliance with international standards, and the embracement of modern technologies, industry professionals continue to advance the operational excellence of gantry crane systems. The reliability and proficiency embedded in every beam design make it a cornerstone of safe and effective lifting operations worldwide.