Having worked in the industrial and manufacturing sector for over two decades,
I have gained extensive hands-on experience with crane girders and gantry girders. These crucial components form the backbone of heavy lifting and material handling systems across various industries, from construction to shipbuilding. Investing in high-quality girders can significantly enhance operational efficiency, safety, and longevity of equipment.
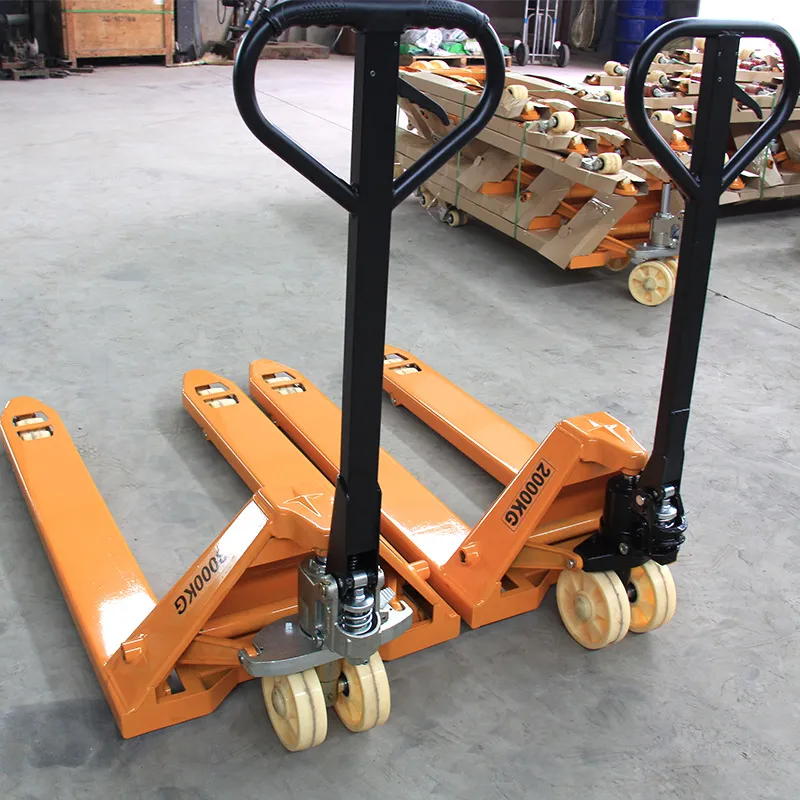
Crane girders are horizontal beams that support the overhead crane's trolley and hoists. These girders need to endure vast amounts of stress, as they must support dynamic loads while accommodating the crane's movement. Typically made of reinforced steel or other high-strength materials, crane girders are crucial for ensuring stability and safety during lifting operations. Their design varies depending on the specific crane system and the load it needs to carry. The precision in fabrication is vital; thus, selecting a manufacturer with a proven track record in quality and compliance with industry standards is non-negotiable.
On the other hand, gantry girders support gantry cranes, which operate on a set of rails mounted on gantries or legs, extending their flexibility and utility in various settings. These are commonly used in shipyards, warehouses, and open yards where overhead crane systems are impractical. Gantry girders must be engineered for outdoor conditions, often requiring additional treatment to resist weather-related wear and tear.
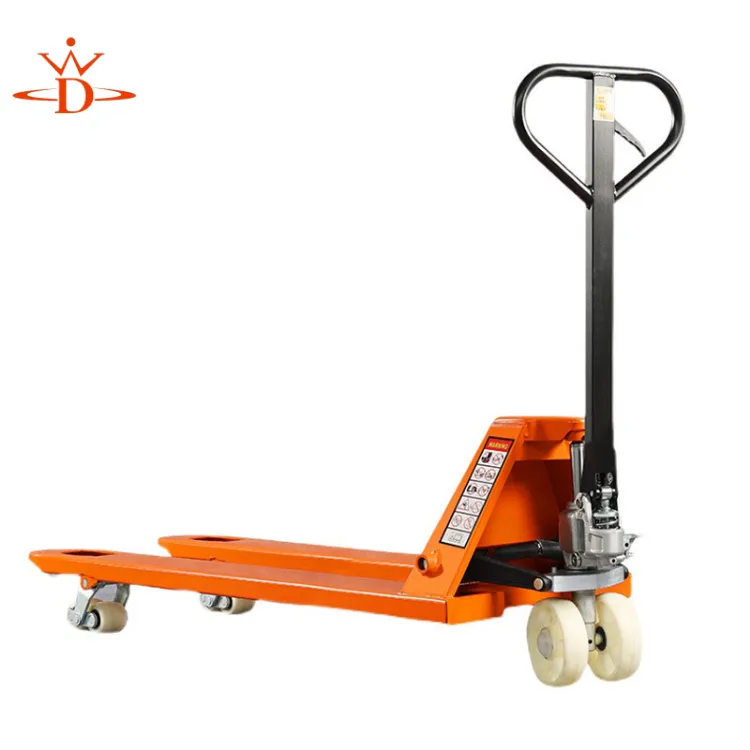
From the lens of an engineer, expertise in the material composition and load-bearing calculations is crucial when dealing with these girders. Choosing the appropriate grade of steel, for example, impacts not only the weight they can handle but also their susceptibility to bending and wearing over time. A key aspect is the girder's deflection—the degree to which it can bend under load without causing mechanical failure or compromising safety. Extensive simulations and stress testing are conducted to ensure these girders meet stringent safety standards.
crane girder and gantry girder
Moreover, an authoritative supplier will offer comprehensive customization options. This is particularly essential as each industrial setting presents unique challenges—be it space restrictions, load requirements, or environmental conditions. Providers with a robust portfolio and ISO certifications often demonstrate a commitment to excellence and adherence to global quality standards, factors that decisively influence purchasing decisions.
In terms of trustworthiness, understanding the supply chain of girder materials ensures that the steel or alloy used is sourced responsibly and meets environmental standards. This due diligence guards against subpar materials that might undermine the girder's integrity, leading to catastrophic failures and potential liabilities. Additionally, regular maintenance schedules and inspections are vital to preserve the girders' operational health, a service often provided by reputable manufacturers as part of their post-sales support.
Ultimately, ensuring the efficiency and safety of lifting operations is not just about the immediate benefits but also about long-term reliability and sustainability of infrastructure investments. Industrial decision-makers are therefore advised to not only consider the immediate cost but also the total cost of ownership which includes maintenance, downtime risks, and system upgrades over the product's lifecycle.
Choosing the right crane and gantry girders is a complex decision that intersects engineering insights, supplier reliability, and strategic foresight. It requires deep industry knowledge, access to innovative design solutions, and a commitment to safety and quality from all stakeholders involved. Investing time in selecting the right partner can yield dividends in operational excellence, safely anchoring your business's growth and resilience.