In the world of heavy lifting and material handling, the 12 gantry crane stands out as an indispensable piece of equipment, known for its remarkable versatility and strength. Industries ranging from construction to shipping and logistics rely heavily on these cranes to move massive loads with precision and efficiency. Here's an in-depth look into the world of the 12 gantry crane, detailing its applications, advantages, and what makes it a pivotal component in modern industry.
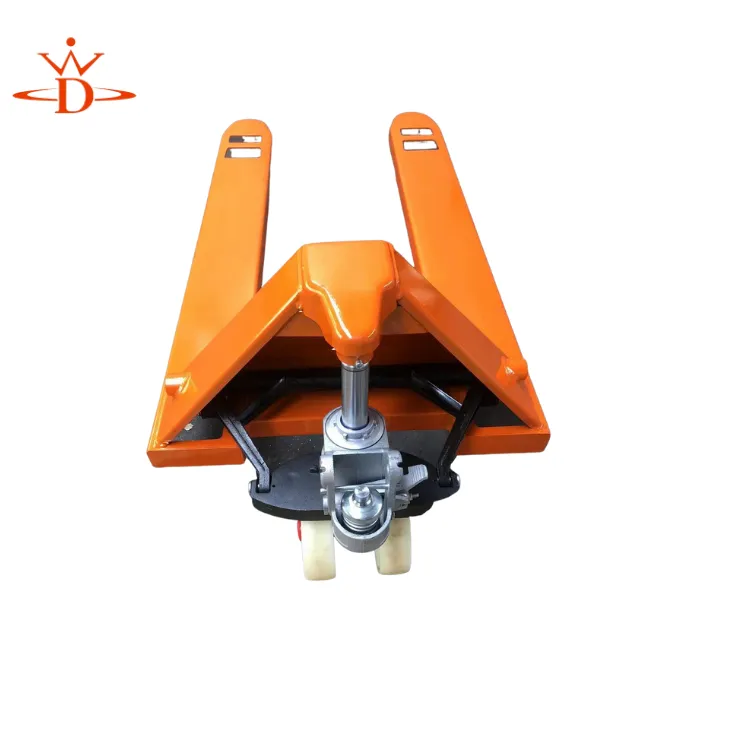
A 12 gantry crane is primarily defined by its ability to lift loads weighing up to 12 tons. This capacity determines its classification as an industrial workhorse, separate from smaller, pedestrian-grade cranes. With its robust design, a 12 gantry crane is engineered to handle the strenuous demands of industrial tasks.
Its structure, typically comprising a horizontal gantry beam supported by vertical legs on each side, offers stability and strength. It's not just about lifting; it's about doing so continuously and reliably, day in and day out.
The applications of a 12 gantry crane are vast and varied. In shipyards, they deftly handle shipping containers, while in construction sites, they might be seen lifting heavy building materials or prefabricated sections of structures. Overhead installations in manufacturing plants often rely on these cranes to move machinery or large components needed on the production line. Their design allows them to cover expansive factory floors or work areas, making them essential for operations requiring precise, repetitive movement of heavy items.
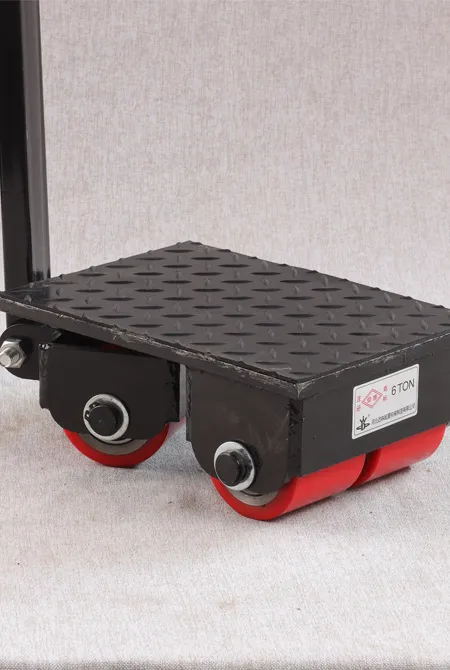
The expertise needed to operate a 12 gantry crane cannot be understated. Operators must be well-trained, not only in the mechanical aspects of the crane but also in understanding load dynamics and safe operation protocols. This training ensures that the crane can be used to its fullest potential without compromising safety. Regular maintenance, overseen by skilled technicians, ensures longevity and operational reliability, making the crane a cost-effective investment over time.
Safety is paramount in any industrial setting, and the 12 gantry crane is no exception. These cranes are equipped with a variety of safety features including emergency stop functions, overload sensors, and precise load movement controls. These features collectively safeguard both the equipment and personnel, reducing the likelihood of workplace incidents.
12 gantry crane
From an expertise viewpoint, the engineering behind a 12 gantry crane is a testament to advanced industrial design. The materials used in the construction of these cranes are carefully selected for their strength and lightweight properties, usually high-strength steel, ensuring the rigidity necessary to handle heavy loads without excess self-weight that might reduce mobility or lift capacity. Their modular design allows for customization, where the length of the gantry, the height of the legs, and the specific hoisting mechanism can be tailored to the needs of a particular application.
Authoritativeness in the industry often comes from leading manufacturers known for their state-of-the-art design and reliability. Companies producing these cranes typically have decades of experience, refining their products through continuous research and development. Brands that consistently deliver high-quality cranes gain reputations as industry leaders, their names synonymous with safety and efficiency.
Lastly, the trustworthiness of a 12 gantry crane comes from both its mechanical reliability and the business ethics of its producers. Trust is built over years of consistent performance, during which cranes must meet and exceed international safety standards while adapting to the evolving needs of their users. Manufacturers with transparent business practices and a commitment to customer service maintain the highest levels of trust with their clients.
In conclusion, the 12 gantry crane is a paragon of industrial capability, from its design to its operation. It plays an indispensable role in various sectors, providing the necessary strength, safety, and precision required in heavy load handling. As industries continue to expand and evolve, the importance of such reliable equipment only grows, driving technological advancements and setting new standards in efficiency and safety.